
MÉCANIQUE
////////////////////////////////////////////////////
Suite à des expériences dans des PME industrielles (Chef d’entreprise, Bureau d’études & Méthodes …), nous nous sommes heurtés à de nombreuses occasions à des soucis de délais de fabrication, des coûts de réalisation de prototypages exorbitants et des rendus ne correspondant pas forcément aux besoins.
De plus, la sous-traitance difficilement maîtrisée en termes de délais, coûts et qualité provoque une perte de savoir-faire qui peut être nuisible voire fatale aux petites structures dont la maîtrise du produits et des processus de conception / fabrication se doit d’être d’autant plus grande que la taille de la structure est petite.
Les projets techniques innovants comportant de plus en plus de produits / processus complexes nécessitant des frais d’outillages importants, il nous est apparu évident que même de petites structures se devaient de passer par une phase de prototypages / fabrication de microséries.
Les Besoins dans le cadre de cette typologie d’activité se portent donc sur une ou des machines ayant les capacités suivantes :
-
Impression 3D de taille Moyenne (environ 400 mm * 400mm * 400mm) avec des niveaux de précision / rendus acceptables permettant de pré-prototyper une pièce en Plastique (type ABS). Ce Pré-prototype permettant de valider un concept / produit avant de lancer des prototypes fonctionnels (avec des processus techniques plus lourds & coûteux permettant eux de faire des assemblages finaux de pièces).
-
Usinage 3 axes et 5 axes permettant de réaliser des pièces mécaniques techniques unitaires ou multi-unitaires en matières plastiques et/ou aluminium de taille moyennes conséquentes (300mm* 300mm *200mm) avec des niveaux de précision +/- 0.1mm. Les temps de réalisation de telles pièces n’étant pas un critère à prendre en compte pour des prototypes ou des micro-séries.
-
Scanner 3D avec des niveaux de précision +/-0.5mm permettant de générer un fichier informatique 3D d’objets existant. Ceci permettant, dans le cadre d'une rétro-ingénierie, de retravailler un produit pour l’améliorer ou le modifier.
Cette machine se devant sur le plan général de sa conception d’être :
-
Simple d’utilisation,
-
Peu coûteuse à l’achat et à l’entretien,
-
D’un encombrement le plus réduit possible pour pouvoir trouver sa place dans de petites entreprises, des bureaux d’études, etc.
-
Équipée d'une Interface Homme Machine ergonomique et sans fioriture
Choix technologiques
//////////////////////////////////////////////////////////////////////
Structure mécanique :
a. Détermination des efforts "maximum" admissibles par la machine :
Voici les calculs des efforts de coupe dans les conditions les plus éprouvantes pour la machine que nous nous sommes fixés.
Fraise diamètre 3mm 2 dents avec les 2 dents en prise simultanément.
Matériau à usiner : Aluminium 7015
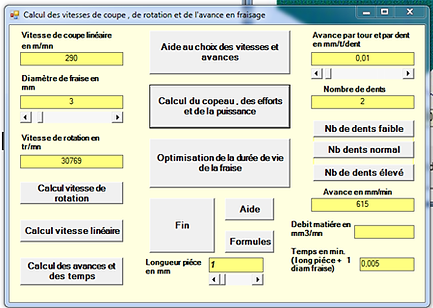
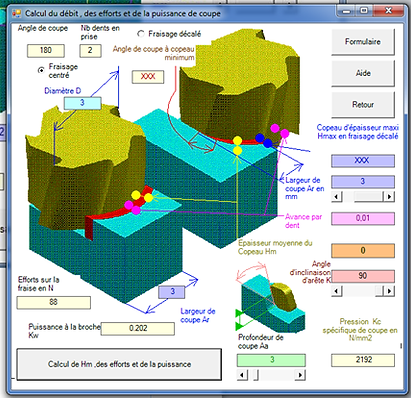
Efforts au droit de l'outil environ 90N
Nous estimons, en prenant un coefficient de sécurité de 4 pour une machine comme celle-ci, que les efforts retenus sont largement pris en considération.
Les intégrations de ces efforts sur les structures permettent de faire des tests avec une méthode des éléments finis nous permettant de valider nos solutions technologiques.

Déplacement Nodal sous charge de 350N localisée au droit de l'effort de coupe maximum de 0.0485mm

Contrainte de Von Mises maximale très inférieure à la limite élastique =
pas de rupture ni de déformation plastique
b. Principe de conception & réponse technologique retenue :
D'une manière générale, dans le cadre de notre machine multifonctions, une conception la plus rigide possible a été retenue. La rigidité se devant d'être la plus grande possible afin de :
-
D'élever la fréquence propre de la machine et de diminuer ainsi l’amplitude des vibrations,
-
D’améliorer la précision des mouvements internes (Tx, Ty et Tz ainsi que Rx, Ry et Rz),
-
Diminuer l’émission de bruits de la machine,
-
Augmenter la rigidité massique en concevant / réalisant une construction légère mais offrant tout de même une rigidité et une résistance suffisantes élevant ainsi la fréquence propre de la machine.
Le choix technologique concernant la structure mécanique s’est porté sur une structure mécanique conçue et réalisée à partir de profilés aluminium standardisés Bosch 20mm * 20mm.
Ces profilés sont légers (aluminium extrudés) avec des sections optimisées en terme d’ergonomie, de moment d’inertie relativement eu égard la masse du profilé. De plus en depit de la simplicité des technologies de liaisons celles-ci permettent toutefois de réaliser des connexions supportant de fortes charges statiques & dynamiques.
Ils permettent une construction rigide, dans la limite du raisonnable grâce à une conception simple mais ambitieuse.
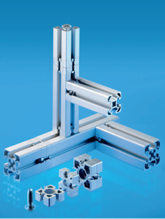
Profilés aluminium

Profilé type Bosch 20mm * 20mm
Technologies de guidages en translation :
Le choix des guidages en translation s’est porté sur une technologie de rail aluminium linéaire de type Open Rail avec des roues Delrin V

Open Rail
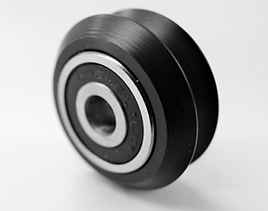
Roue Delrin V
Ces produits ont retenu notre attention car simples à mettre en œuvre, efficaces avec des caractéristiques de résistance mécanique (résistance à la compression de 63 MPA), la perméabilité aux liquide...
Dans le cadre des pré-études, les choix primaires nous ont donc imposé les contraintes suivantes :
-
Choix de matériaux de construction légers ayant les module d’élasticité les plus élevés possible (nécessité de rester dans le cadre de l’élasticité du matériau pour éviter les déformations résiduelles du domaine plastique…),
-
Avoir des poutres avec des moments quadratiques les plus important possible tout en conservant des nervures afin d’éviter le phénomène de voilement/déversement latéral (Eloigner autant que faire se peut la matière de la fibre neutre de la poutre en conservant des nervures).

Structure nervurée formant une coque formée de plaques à nervure liées
l'ensemble formant un bâti fermé

Augmentation des moments quadratiques sur les poutres du portique
les plus susceptibles de « recevoir des efforts » lors des actions d'usinage

Les zones supportant les contraintes les plus importantes ont été conçues sur la base de poutres treillis permettant d'avoir, dans le cas des « poutres principales » des éléments porteurs solides et rigides
-
Fermer autant que faire se peut les profils et les sous-ensembles pour contrecarrer les efforts de torsion
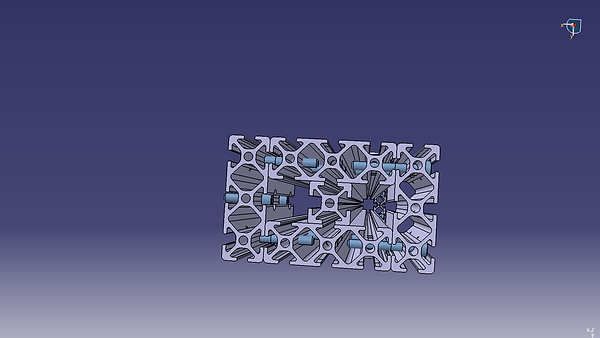
Création de poutres fermées à moment quadratique élevé pour un poids le plus faible possible
-
Cloisonner les bâtis et les caissons
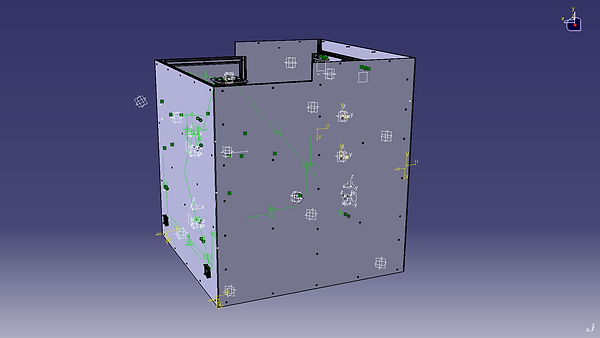
Bâti fermé sur 5 côtés
-
Faire passer les forces par les centres / axes de torsion ou le plus près possible de ceux-ci
-
Prévoir des liaisons isostatiques ou avec des degrés d'hyperstaticité les plus faibles possible pour éviter des coûts de fabrication trop importants, des difficultés de montage, ainsi que des efforts résiduels dans les systèmes, engendrant des usures prématurées.

Montage des roues de guidage sur excentrique pour assurer un guidage « doux »

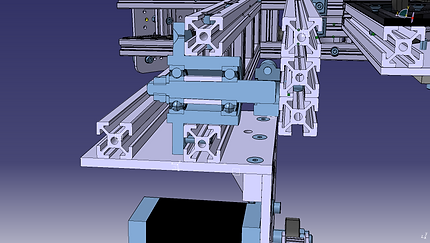
Paliers longs doubles, pour les axes Rx et Ry, sur blocs assurés par des roulements à billes à gorges profondes